đź•‘ Reading time: 1 minute
Cell-filled concrete pavement is the technology developed by IIT Kharagpur, which has proved to be a very promising solution for overloaded vehicles, inadequate drainage facilities, and waterlogging problems. Cell-filled concrete pavement consists of formwork of plastic cells over the compacted subgrade / sub-base, filled with concrete or stones.
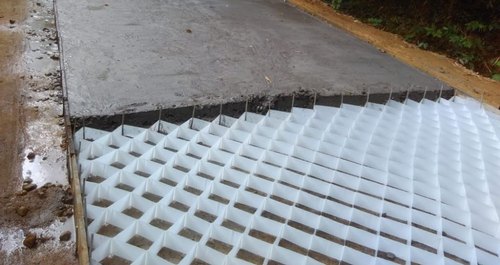
This article discusses the components, construction procedure, advantages, and disadvantages of cell-filled concrete pavement.
Contents:
Components of Cell filled Concrete Pavement
1. Plastic Cells
The plastic cells act as both the form and reinforcement for the pavement. The plastic cells are made from reclaimed high-density polyethylene (HDPE) sheets of thickness 0.22 mm to about 0.25mm. These plastic cells can be supplied as rolls of strips 50mm to 100mm wide, depending upon the depth requirement. The strips can be heat-welded or stitched to form cells.

A pair of strips can be welded at 300 mm intervals. The third strip is welded to the first pair at 300 mm intervals so that the stitch lies at the center of the previous stitching. The third and the fourth ones are again welded like the first two. Figure 4 shows the plan of a cell.
2. Subgrade
The subgrade forms the top 300 mm thick portion of the embankment. The embankment subgrade is compacted in two layers, usually to a higher standard than the embankment. If the embankment soil is poor, the top 300mm of the subgrade may consist of good quality material from borrow pits with CBR exceeding five. The subgrade shall be compacted to at least 100 percent of Maximum Dry Density per IS:2729 (Part 7). The expansive black cotton soil (BCS) should be compacted to a minimum of 95% of the maximum dry density with moisture content 2% higher than the optimum.
The subgrade soil of existing roads is expected to have attained the required stability due to traffic, and the CBR test should be done at in situ dry density and moisture content after four days of soaking. A dynamic cone penetration test is carried out to determine CBR values of subgrade quickly, and CBR values corresponding to soaked condition can be obtained from records of similar soils.
3. Subbase
The subbase consists of laterite boulder consolidation, water-bound macadam, wet mix macadam, crusher run macadam, lime-fly ash-aggregate mixtures, lime stabilized soil, cement stabilized soil, and others with proprietary stabilizers. Locally available aggregates such as murrum and kankar mixed with lime fly ash may also be used. The locally available materials such as natural gravel/soil aggregate or blended with suitable aggregate fractions of stone, gravel, moorum, sand, or a combination of these materials depending on the grading required.
If the number of commercial vehicles is more than fifty per day, 150mm of cementitious sub base with a minimum 7-day strength of 1.5 MPa is recommended. The subbase should be provided with stone/concrete block, or Brick on edge should be laid on either side of the carriageway projecting 50 to 100 mm above the subgrade/subbase for the confinement and protection. Stone/ concrete block or Brick on end edge should be laid on either side of the carriageway projecting 50 to 100 mm above the subgrade/subbase for confinement and protection.
4. Concrete
Conventional pavement concrete with 28-day strength of 30 MPa with a slump of about 30 to 50mm can fill up the cell. Super-plasticiser should be used to reduce water requirements for the desired slump. The Roller Compacted Concrete (RCC), as specified in clause 1502 of Specifications for Rural Roads, can also be used for filling up the plastic cells and compacted with a roller.
Construction Procedure of Cell-filled pavement concrete.
- The construction of embankment, subgrade, and subbase should be done as per Specifications for Roads.
- A proper camber as applicable to rural roads shall be provided. Drainage layer should be provided in high rainfall areas (annual rainfall exceeding 1000 mm) as laid down in Road Manual.
- Stone/concrete block or Brick on end edge should be laid on either side of the carriageway projecting 50 to 100 mm above the subgrade/subbase for the confinement and protection of cell-filled concrete.
- A hard shoulder with proper cath is necessary for the concrete blocks' stability since trucks traveling close to the edge may damage the unconfined concrete blocks.
- The width of the hard shoulder should be about 0.85 m on either side of the pavement.
- Formwork of plastic cells shall be laid across the compacted subbase and put under tension with iron spikes so that cells are close to squares in plan.
- Nylon threads passing at 10 mm below the top of the cells shall prevent the cells from collapsing while filling the cells with concrete.
- If any stitch of the cells opens up during tensioning, it should be stapled near the top, middle, and bottom.
- The concrete shall be filled into the cells to a depth of 120 mm, which is about 20 mm higher than the cell's depth.
- The iron spikes shall be removed after the cells are filled up with concrete. For RCC, two passes of the roller in static mode followed by two passes in vibratory and another pass in static mode shall be sufficient compaction and a good finish.
- The number of passes in static and dynamic modes depends upon the texture of aggregates and moisture content.
- Pan vibrators can be used to compact the conventional concrete having a slump of about 30 to 40 mm.
- The number of roller passes, the amplitude of vibrations, the depth of loose concrete in cells, and the amount of water to be added shall be determined from the trial run.
- The concrete's surface shall be covered with wet jute mats or paddy straw to prevent drying during hot weather.
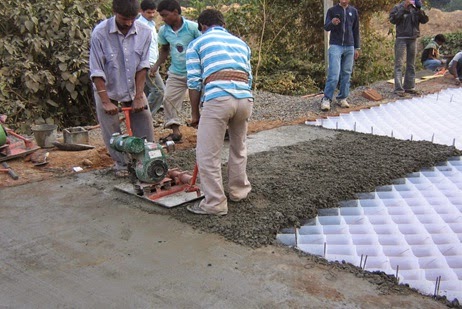
Curing
As the camber of 3 to 3.5 % is given for rural roads- wet jute/coir mats and wet paddy straw shall provide better water curing option and light traffic to move on the surface. Water accumulates on the lower side of the mud enclosure in the water ponding method, whereas the higher part becomes dry soon.
Advantages of Cell Filled Concrete Pavements
- Use of recycled plastic.
- As the expansion or contraction joints are not required, and hence maintenance of joints is eliminated.
- The cost of construction is considerably reduced when compared to conventional cement concrete pavement.
- The consumption of aggregates is almost reduced to 50% when compared to normal CC pavements.
- If the individual block fails, it can be easily replaced without much effort and with the least cost.
Disadvantages of Cell Filled Concrete Pavements
- The preparation of the cells is cumbersome.
- There are high chances of cells getting disturbed while placing the concrete, and hence proper care is required.
- Due to slow progress, the men and machinery's efficiency is less than the normal construction.
Read More:
Continuously Reinforced Concrete Pavement – Characteristics, Construction, and Comparison
Types of Concrete Pavements -Their Construction Details and Applications
Concrete Resurfacing – Repair of Concrete Floor or Pavement Surfaces